1. 射出成型の基礎知識
1-1. 射出成型とは何か
・射出成型の定義と基本プロセス
射出成型は、プラスチック材料を加熱して溶融状態にし、高圧で金型に射出して成型する製造プロセスです。
このプロセスは、金型内で冷却・固化することで、複雑な形状の製品を高精度かつ大量に生産できます。
基本的なプロセスは材料準備、溶融、射出、冷却、取り出し、仕上げのステップから成ります。
・歴史と発展
射出成型の歴史は19世紀後半に遡り、最初の射出成型機は1872年に発明されました。
プラスチック材料の進化とともに、射出成型技術も進化し続け、現在では自動化やデジタル技術の導入により、さらに高度な製品製造が可能になっています。
1-2. 射出成型の利点と欠点
・射出成型のメリット
射出成型の主な利点には以下があります。
高精度:
複雑な形状や細部も正確に成型できます。
高速生産:
大量生産が可能で、生産サイクルタイムが短いです。
低コスト:
一度金型を作れば、製品一つあたりのコストが低くなります。
多様な形状:
幅広い形状やサイズの製品を成型できます。
・射出成型のデメリットとその克服方法
初期費用が高い:
金型の製造には高い初期投資が必要です。
【対策】大量生産によって初期コストを分散する。
材料の制約:
特定のプラスチック材料に限定される場合があります。
【対策】 材料科学の進歩により、新たな素材の開発が進んでいます。
不良品の発生:
成型不良が発生することがあります。
【対策】 プロセス管理と品質検査を徹底する。
1-3. 使用されるプラスチック材料
・ポリエチレン(PE)
ポリエチレンは、軽量で耐薬品性があり、食品包装や医療製品などに広く使用されます。
低密度ポリエチレン(LDPE)と高密度ポリエチレン(HDPE)の二種類があります。
・ポリプロピレン(PP)
ポリプロピレンは耐熱性が高く、家庭用品や自動車部品に使用されます。
透明性があり、また耐薬品性も優れています。
・その他の一般的な材料
ポリスチレン(PS):
透明性が高く、使い捨て容器や家電製品の筐体に使用されます。
ABS樹脂:
高強度で、家電製品や玩具、自動車部品に使われます。
ポリアミド(ナイロン):
高強度と耐熱性を持ち、機械部品や電子部品に使用されます。
1-4. 射出成型機の基本構造
・射出成型機の主要なコンポーネント
射出成型機は、以下の主要なコンポーネントから構成されます。
ホッパー:
材料を供給するための装置。
スクリュー:
プラスチックを溶融し、混合して金型に送り出す螺旋状のシャフト。
バレル:
プラスチックを加熱するシリンダー。
金型:
成型する製品の形状を決定する金属製の型。
クランプユニット:
金型を固定し、成型時の圧力に耐えるための装置。
・機械の種類とその特徴
油圧式成型機:
強力な圧力を提供し、大型部品の成型に適しています。
電動式成型機:
エネルギー効率が高く、高精度な成型に適しています。
ハイブリッド成型機:
油圧式と電動式の利点を組み合わせたタイプです。
1-5. 射出成型の応用分野
・自動車産業
自動車部品の多くは射出成型によって製造されています。
バンパー、ダッシュボード、ドアパネルなどが例として挙げられます。
・家電製品
テレビの筐体、冷蔵庫の内部パーツ、洗濯機の部品など、家電製品の多くは射出成型で作られています。
・医療機器
シリンジ、キャップ、容器、その他の医療用プラスチック部品も射出成型で製造されます。
高い精度と衛生管理が求められる分野です。
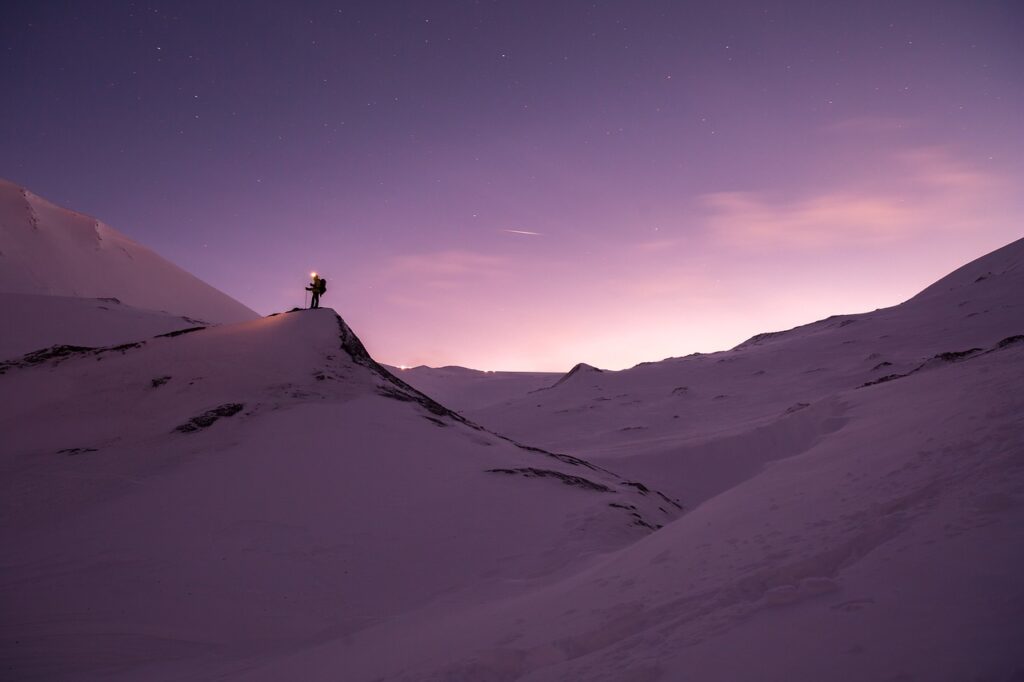
2. 射出成型のプロセス詳細
2-1. 材料の選定と準備
・プラスチックペレットの特性と選び方
射出成型で使用するプラスチック材料はペレット状になっています。
選定する際には、以下の特性を考慮します。
機械的特性:
強度、硬度、靭性
熱特性:
熱変形温度、ガラス転移温度
化学的特性:
耐薬品性、吸湿性
コスト:
材料費、加工費
・ホッパーと材料の供給
ペレットはホッパーに投入され、一定の供給量を維持しながら成型機に送られます。
ホッパー内での乾燥処理が必要な場合もあり、材料の吸湿性に応じてデシカントドライヤーなどが使用されます。
2-2. プラスチックの溶融と混合
・スクリューの役割
スクリューは射出成型機の中核であり、ペレットを前進させながら加熱・溶融します。
スクリューの設計(長さ、直径、ピッチ)は、材料の種類や成型品の要求に応じて最適化されます。
・溶融温度と圧力の管理
プラスチックを均一に溶融するために、適切な温度と圧力の管理が必要です。
バレル内のゾーンごとに異なる温度設定を行い、溶融温度を最適化します。圧力は材料の流動性と射出速度に影響を与えます。
2-3. 金型への射出と成型
・金型の設計と製造
金型の設計は成型品の品質に直結します。
流路、ゲート、ランナー、冷却系統の設計が重要です。金型は通常、鋼やアルミニウムで作られ、製造にはCNC加工やEDM(放電加工)が使用されます。
・射出のプロセスとその制御
溶融プラスチックはスクリューによって高圧で金型に射出されます。
この過程では、射出速度、圧力、温度を細かく制御し、成型品の均一性と品質を確保します。充填が完了した後、保持圧をかけて成型品の寸法精度を高めます。
2-4. 冷却と固化の重要性
・冷却システムの設計
冷却は成型サイクルの中で重要なステップです。金型内には冷却水が循環し、効率的に熱を取り除きます。
冷却系統の設計には、冷却チャネルの配置や流速の最適化が含まれます。
・冷却時間の最適化
冷却時間は成型サイクルの効率に直接影響します。
冷却が不十分だと成型品の寸法精度や外観に問題が生じるため、適切な冷却時間を設定する必要があります。冷却時間の短縮には、材料特性や金型設計の工夫が必要です。
2-5. 成型品の取り出しと仕上げ
・自動取り出しシステム
冷却・固化した成型品は金型から自動取り出し装置(ロボットアームやエジェクターピン)によって取り出されます。
このステップは、成型品の表面に傷をつけずに迅速に行うことが重要です。
・ゲートやバリの処理方法
成型品にはゲート跡やバリが残る場合があります。
これらは後工程で手作業や自動機器を使って取り除かれます。トリミングやデバリング(バリ取り)によって成型品の仕上げが行われます。
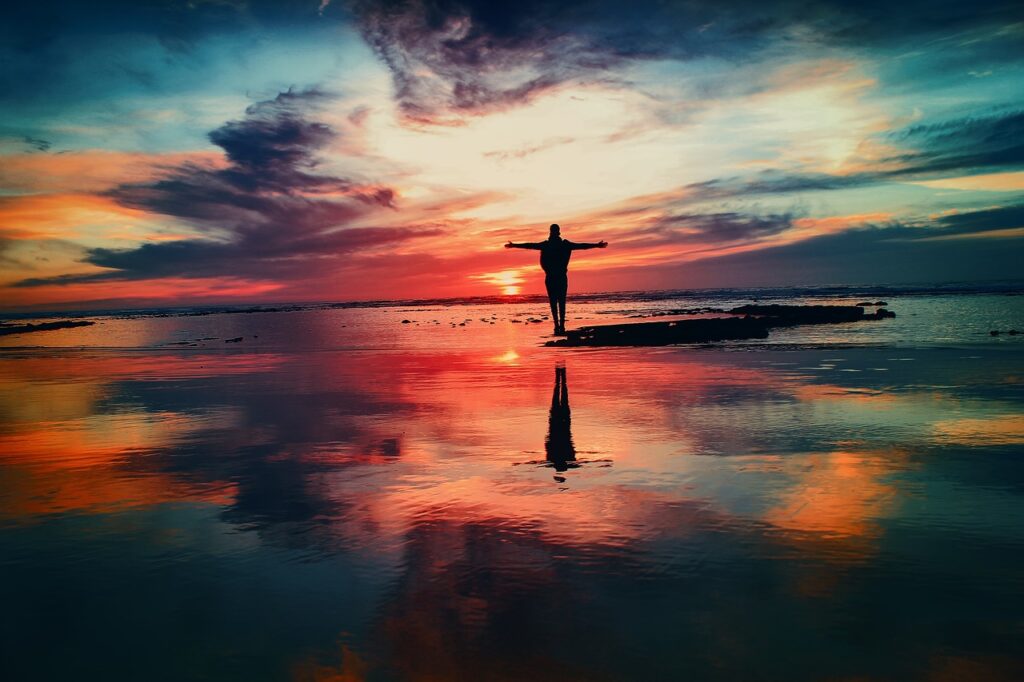
3. 射出成型の機械と設備
3-1. 射出成型機の種類
・油圧式成型機
油圧式成型機は、高圧を発生させるために油圧システムを使用します。
大きな力を発揮できるため、厚みのある大型部品や高強度が求められる製品の成型に適しています。
特に、射出圧力やクランプ力の調整が容易で、幅広い材料や製品に対応できますが、エネルギー消費が多いのが難点です。
・電動式成型機
電動式成型機は、電気モーターを使用してスクリューの駆動やクランプ動作を行います。
高精度かつ高速な動作が特徴で、エネルギー効率が非常に高いです。射出速度や圧力の制御が正確で、薄肉成型や複雑な形状の成型に適しています。
メンテナンスが比較的簡単である点も利点です。
・ハイブリッド成型機
ハイブリッド成型機は、油圧式と電動式の両方の利点を兼ね備えた成型機です。
例えば、クランプ動作には油圧を、射出動作には電動モーターを使用することで、効率とパフォーマンスのバランスをとっています。
これにより、エネルギー効率を保ちながら、高い射出圧力が必要な成型にも対応できます。
3-2. 射出成型機の選定基準
・生産量と精度
射出成型機を選定する際には、求められる生産量と製品の精度が重要な基準となります。
大量生産が必要な場合は、高速で安定した動作が可能な機械が必要です。
また、高精度が求められる製品には、細かい制御が可能な電動式成型機が適しています。
・コストと効率
初期投資、運用コスト、エネルギー消費などのコスト要因も選定基準です。
エネルギー効率が高い電動式成型機は、運用コストの削減に貢献しますが、初期費用が高くなることもあります。
製品の特性と生産条件に合わせて、最適なバランスを見つけることが重要です。
3-3. 金型設計と製造
・金型材料の選定
金型は通常、高耐久性の鋼やアルミニウムで作られます。
鋼製の金型は長寿命で高精度な成型に適していますが、製造コストが高くなります。
アルミニウム製の金型は軽量でコストが低く、小ロット生産やプロトタイプ製作に向いています。
・金型の寿命とメンテナンス
金型の寿命は、材料、設計、使用条件によって異なります。
定期的なメンテナンスが金型の寿命を延ばし、成型品の品質を維持するために重要です。
金型の清掃、潤滑、摩耗部品の交換などが定期的に行われるべきです。
3-4. 付随設備と補助機器
・ホッパードライヤー
ホッパードライヤーは、プラスチックペレットの乾燥に使用されます。
湿気を含む材料は成型不良の原因となるため、成型前にペレットを乾燥させることが重要です。
・温調機
温調機(温度制御機)は、金型の温度を制御するために使用されます。
適切な温度管理は、成型品の品質に直接影響します。温調機は、金型内部の冷却水や加熱油の温度を一定に保ちます。
・ロボットアーム
ロボットアームは、成型品の取り出しや次工程への搬送、自動化ラインの一部として使用されます。
自動取り出しにより、成型サイクルの短縮と人件費の削減が可能になります。
3-5. 最新の技術動向
・IoTとスマート成型機
IoT技術の導入により、射出成型機のデータをリアルタイムで監視・解析することが可能になりました。
これにより、予知保全や生産性の向上が実現します。スマート成型機は、データ駆動型の管理と制御が可能で、品質管理の自動化が進んでいます。
・自動化とロボティクス
成型プロセスの全自動化が進んでおり、ロボティクス技術を駆使して人手を介さずに成型から仕上げまでの工程が行われるようになっています。
これにより、生産効率の向上と品質の安定が期待されています。
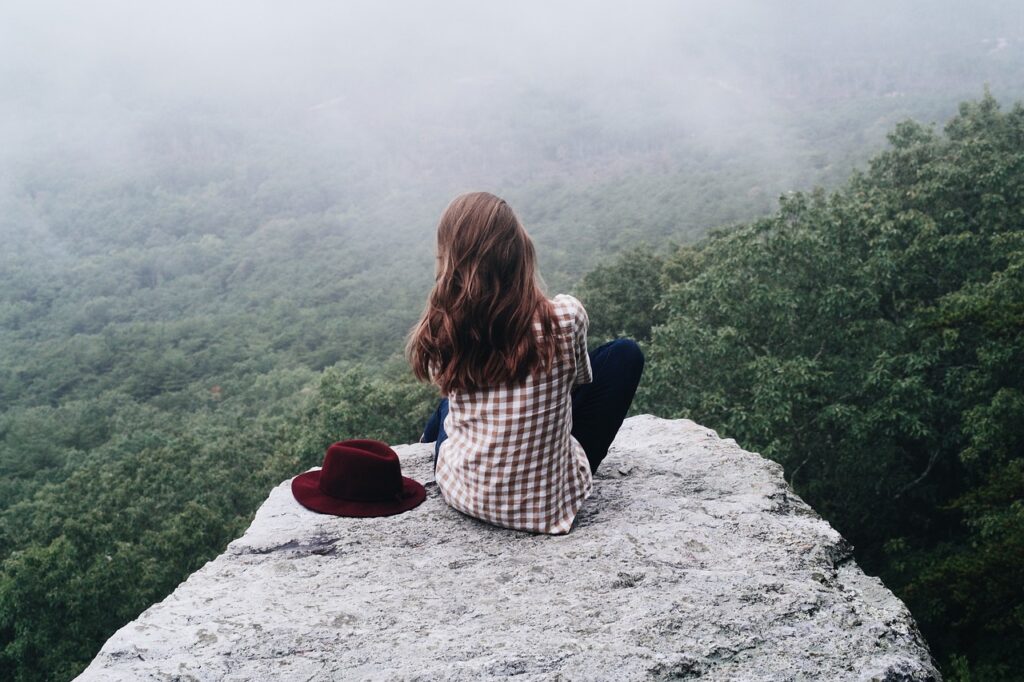
4. 射出成型のトラブルシューティング
4-1. 一般的な成型不良とその原因
・ショートショット
ショートショットとは、成型品が完全に充填されずに部分的に欠ける現象です。
主な原因として、射出圧力不足、射出速度の遅さ、金型内の空気の逃げ場不足が考えられます。
また、材料の流動性が低い場合や、溶融温度が不十分な場合にも発生します。
・フラッシュ(バリ)
フラッシュは、成型品の合わせ目から材料がはみ出す現象です。
主な原因は、金型の合わせ面の密閉不良、射出圧力が高すぎること、金型の磨耗や変形です。
また、過剰な材料供給や、クランプ力不足も原因となります。
・ウェルドライン
ウェルドラインは、材料が金型内で合流する際に形成される線状の痕跡です。
主な原因として、材料の温度が低すぎること、射出速度が遅いこと、金型の温度が低いことが挙げられます。
ウェルドラインは、強度低下や外観不良の原因となるため、注意が必要です。
4-2. 成型不良の解決方法
・材料の調整
成型不良を解決するためには、材料の特性を見直すことが重要です。
例えば、流動性の高い材料を選定する、適切な乾燥時間を確保する、添加剤を調整するなどの方法があります。また、再生材料の使用量を適切に管理することも効果的です。
・機械設定の見直し
射出成型機の設定を調整することで、不良を減少させることができます。
具体的には、射出速度、射出圧力、保持圧、溶融温度、金型温度の調整が考えられます。これらのパラメータを最適化することで、成型不良の発生を防止できます。
・金型の改良
金型自体の設計やメンテナンスを見直すことも重要です。
例えば、空気抜きの位置や数を増やす、冷却チャネルの配置を最適化する、金型の合わせ面の密閉性を向上させるなどの方法があります。定期的なメンテナンスも欠かせません。
4-3. 品質管理と検査方法
・視覚検査
視覚検査は、成型品の外観品質を確認するための基本的な方法です。
目視による検査はもちろん、自動視覚検査システムを導入することで、より効率的かつ正確に外観不良を検出できます。
・物理試験と機械試験
成型品の品質を確保するためには、物理試験と機械試験が必要です。
物理試験には、引張試験、圧縮試験、曲げ試験などが含まれます。機械試験では、成型品の寸法精度や表面硬度を測定し、設計通りに製品が仕上がっているかを確認します。
4-4. 成型プロセスの最適化
・プロセスパラメータの調整
成型プロセスを最適化するためには、射出速度、圧力、温度、冷却時間などのパラメータを調整することが重要です。
これらのパラメータを適切に設定することで、成型不良の発生を防ぎ、品質を向上させることができます。
・生産効率の向上
生産効率を向上させるためには、成型サイクルタイムの短縮、材料の無駄削減、エネルギー効率の改善が必要です。
これには、自動化設備の導入や、生産ライン全体の見直しが有効です。また、データ解析によるプロセスの最適化も重要です。
4-5. 予防保全と定期メンテナンス
・機械の定期点検
射出成型機の定期点検は、故障を未然に防ぎ、安定した生産を維持するために不可欠です。
点検項目には、油圧システム、電気系統、冷却系統、スクリューやバレルの状態が含まれます。定期的な清掃や部品の交換も重要です。
・金型の保全
金型は高価で重要な設備ですので、定期的なメンテナンスが必要です。
具体的には、金型の清掃、潤滑、磨耗部品の交換、変形や亀裂の検査が含まれます。定期的なメンテナンスにより、金型の寿命を延ばし、品質を維持することができます。
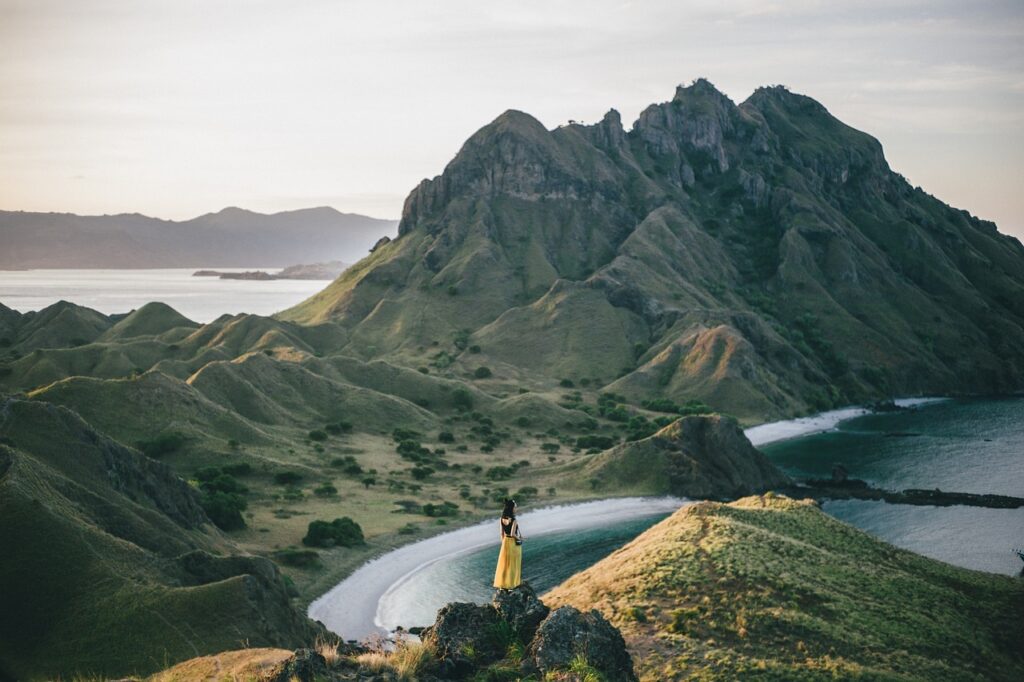
5. 射出成型の未来と展望
5-1. 射出成型の技術革新
・材料技術の進化
射出成型に使用されるプラスチック材料は、絶えず進化しています。
高性能なエンジニアリングプラスチックやバイオプラスチックの開発が進んでおり、これにより成型品の性能や環境負荷の低減が期待されています。
また、ナノコンポジット材料の導入により、強度や耐久性が飛躍的に向上しています。
・プロセスの自動化
射出成型プロセスの自動化が進んでおり、ロボットアームや自動化ラインの導入が一般化しています。
これにより、生産効率の向上と人件費の削減が実現し、品質の均一化も達成されています。将来的には、完全無人化工場も現実のものとなるでしょう。
5-2. デジタル化とスマート製造
・IoTとビッグデータの活用
IoT(モノのインターネット)技術の導入により、射出成型機の運転データをリアルタイムで収集・分析することが可能になりました。
ビッグデータ解析を通じて、プロセスの最適化や予知保全が実現し、生産効率と品質の向上が期待されています。
・AIによる品質管理
AI(人工知能)の活用により、品質管理の自動化が進んでいます。
AIは、射出成型プロセス中に発生する膨大なデータを解析し、不良品の予測やプロセスの改善提案を行います。これにより、人間の介入を最小限に抑えながら、高品質な成型品の生産が可能になります。
5-3. 環境に優しい射出成型
・リサイクル材料の使用
環境意識の高まりにより、リサイクル材料の使用が促進されています。
射出成型では、使用済みプラスチックを再生して新たな製品を作るリサイクル技術が進化しています。これにより、廃棄物の削減と資源の有効活用が実現されます。
・省エネルギー技術
射出成型プロセス自体の省エネルギー化も進んでいます。
エネルギー効率の高い電動式成型機の普及や、プロセスの最適化によるエネルギー消費の削減が行われています。また、再生可能エネルギーの利用も進んでおり、環境負荷の低減が図られています。
5-4. 新たな応用分野の拡大
・医療分野
射出成型技術は、医療分野での応用が拡大しています。
高精度で清潔な製品が求められる医療機器や部品の製造において、射出成型は不可欠な技術となっています。
また、バイオプラスチックの導入により、生体適合性の高い製品の製造も進んでいます。
・航空宇宙分野
軽量かつ高強度の部品が求められる航空宇宙分野でも、射出成型技術が注目されています。
特に、複合材料を使用した部品の製造において、射出成型はその高い成形性と精度が評価されています。
今後、さらなる技術革新により、より多くの部品が射出成型で製造されるようになるでしょう。
5-5. 未来の展望と課題
・技術の標準化と互換性
射出成型技術の進化とともに、技術の標準化と互換性の確保が重要となります。
異なるメーカーや地域間での技術の統一が進むことで、グローバルなサプライチェーンがより効率的に機能するようになります。
・人材育成と教育
射出成型技術の高度化に伴い、専門的な知識と技能を持つ人材の育成が重要です。
教育機関や企業内での研修プログラムの充実が求められます。また、デジタル技術や自動化技術に対応できる人材の育成も課題となります。